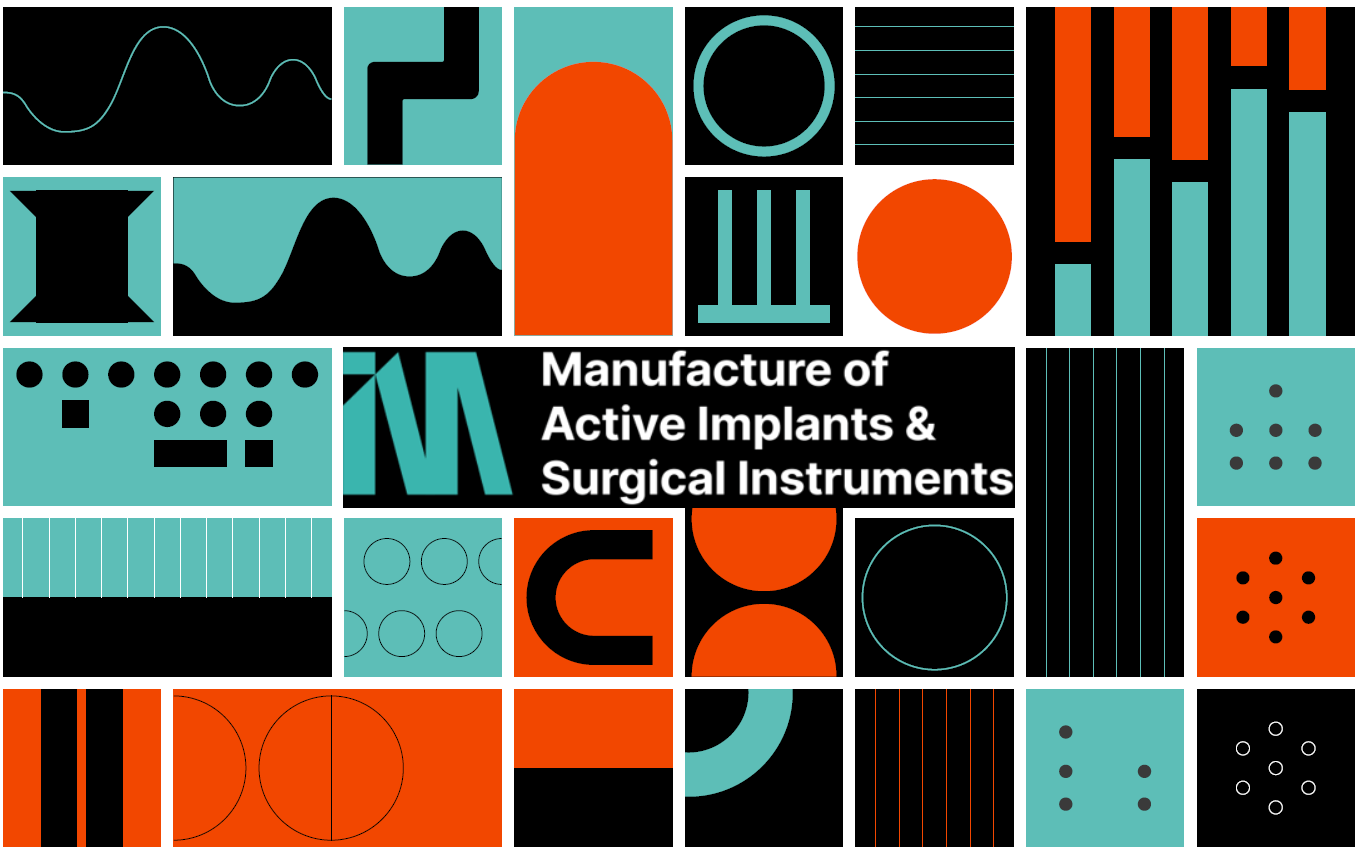
In Conversation: with Anne Vanhoestenberghe from MAISI
MedCity’s Cluster Development Research Associate, Pranetha Baskaran, chats to Anne Vanhoestenberghe, Deputy Director of MAISI (Manufacture of Active Implants & Surgical Instruments)
Last month’s launch of the UK government’s £60 million Life Sciences Innovative Manufacturing Fund focused attention on the need to support scale-up of medtech production nationally, but there is also a need to support device developers at the much earlier prototype stage. We were therefore intrigued to encounter the work of the team at the national MAISI facility during our current scoping work mapping the life sciences community across the London borough of Lambeth.
Part of the emerging medtech hub around St Thomas’s Hospital, MAISI was established by King’s College London School of Biomedical Engineering & Imaging Sciences, in partnership with UCL and Newcastle University, with the support of a Wellcome grant of £5.2 million. Its goal is to accelerate the development and uptake of innovative technologies that improve health outcomes.
Pranetha: I was very excited to discover the MAISI facility and find out about the work you are doing to support medical device innovators. Can you tell us how MAISI came about and what problem it’s solving?
Anne: Absolutely. For complex devices, it takes a lot of expertise and several million pounds worth of investment to build a manufacturing space, and due to the changing regulatory landscape it can take 10-15 years of continuous funding to reach a level where a device can reach the patient. From an industry transfer point of view, a complex device is high risk, so you need to have de-risked it to a level which is very advanced in terms of time and financial commitment. It’s rare to see a device produced by a research team go all the way into patients, yet very few get picked up by industry at the early development stage, researchers need to reach the first tests in humans.
With MAISI we want to address this. The facility is being built inside St Thomas’s Hospital and it will facilitate the work of both academic researchers and small companies. We’re part of KCL and GSTT but we’re dedicated to supporting R&D across the entire UK community when they need prototype manufacture.
There are so many companies and academic researchers who come up with ideas. They will go up to the point where they have a proof of concept on the bench, and then they’re faced with a wall of challenges and they can’t get beyond it. MAISI is going to break down this wall, supporting researchers all the way through to realising an end product. There is huge potential for investment in a device after you’ve de risked it. The challenge is to get there, and that’s what MAISI will enable.
Pranetha: Are there any particular focus areas for the types of medical devices MAISI will support?
Anne: At the moment there’s a lot of innovation in surgical and imaging science that require complex devices which MAISI can produce. There is also exciting research on interfaces with the nervous system – for controlling a prosthesis, for example. There’s also huge amount of work in the UK on artificial organs, and if you create an artificial organ, you still have to somehow interface it with the nervous system. It’s challenging currently to get the organ to directly interface neurologically. So we place active implants that can act like a bridge between the artificial organ, whether you’ve created an artificial muscle or replacement for the body parts that have been affected. So there’s a huge scope for MAISI to support in advancing implantable devices.
Pranetha: What is the timeline for the facility opening and when can researchers and companies come to you? Are you fielding queries already, for example?
Anne: The facility will be operational next year, but we’ve already been contacted by a few companies. In fact, because we know the timelines to develop these devices (three to five years on average), we’re really encouraging people to contact us now. We know that if you can demonstrate visibility, if you can de-risk to a certain stage, you have the potential to attract hundreds of millions in investment. But there’s also another area of devices that may only serve a small number of patients. For those devices, MAISI will enable academic researchers or small start-ups to find a niche market. We’re also there to help the people who may have a different business model and a different prospect of growth. We’re not just there to support the company that’s going to be the next big thing.
Pranetha: And in terms of the commercial offer of MAISI, would companies coming to you pay a fee or would you take a percentage of IP, how would it work on a practical level?
Anne: We will have a charging model, but we will not touch IP. We’re not a design company; we will manufacture devices designed by others, so their IP is completely protected.
Pranetha: So at the moment, companies could come to you for initial conversations about where they are with their product development and next steps before getting into that prototype manufacturing?
Anne: Certainly. Start-ups can contact us with an idea now if they need expertise. We can also help with Innovate UK funding advice, and because we are part of KCL, we have access to a huge list of contacts we can draw on for further support.
Pranetha: From an international perspective, how will MAISI compare to what’s available in Asia or the US, for example?
Anne: As far as I know, there is nothing like MAISI, because it’s not a proposal with commercial value for an external manufacturer to undertake. The reason I think it will work is because I’ve seen so many people being challenged at a time where they just have this last step of manufacturing to do.
We’re only doing small batches, working with you until your product reaches a point where you can do your first study in patients. We think then you’ve been de-risked. You will have everything you need to submit an MHRA application. You also have what you need to go and approach investors who can commit to funding manufacture in larger quantities.
Pranetha: What types of manufacturing equipment will you use – is it bespoke for example? Have you had to adapt some existing technology?
Anne: A lot of what we’re doing will be using traditional manufacturing methods, conceived and used in a way that is appropriate for a very clean environment and for very clean finished products. 3D printing is one element of this. There are issues with 3D printing though, which limits the way we can use it for some stages of the manufacturing process. And then we have some very standard methods, like screen printing and welding, but used to produce the highest-grade electronics. These methods are very well established. We’re just using them in a new way, and therefore we’re slightly rescaling everything we do.
Pranetha: Will international companies also be able to approach you now? Or is there a staged access?
Anne: Initially we want to focus on the UK community, though I wouldn’t discourage international companies from approaching us at this stage. We’re talking to everyone as we’re really interested in understanding what their needs are.
Find out more
For more information please contact maisi@kcl.ac.uk